Cold storage facilities often face the challenge of maintaining temperature control while ensuring efficient movement of people and products. A pivotal solution in addressing this challenge is the installation of cold storage plastic curtains. These specialized curtains, crafted from durable PVC materials, serve not only as temperature barriers but also as facilitators of operational efficiency in refrigerated environments.
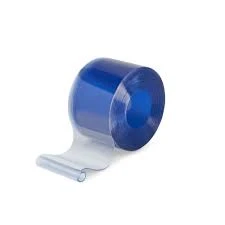
Cold storage plastic curtains, also known as strip doors, are engineered to provide significant energy savings by minimizing temperature fluctuations. The ability of these curtains to maintain the integrity of a controlled environment is crucial in warehouses, food storage facilities, and pharmaceutical warehouses where temperature-sensitive goods are stored. They act as an effective barrier that separates different climate zones without hindering accessibility, allowing personnel and vehicles to pass through with minimal temperature exchange.
Practical experience from cold storage managers highlights the importance of curtain thickness and material quality. It's widely noted that curtains with a thickness ranging from 1 mm to 2 mm strike the perfect balance between durability and flexibility. These curtains not only endure the rigors of daily traffic but also effectively trap cold air within designated areas, reducing energy costs. Furthermore, options in ribbed PVC enhance this durability by reducing scratching and prolonging the curtain's lifespan.
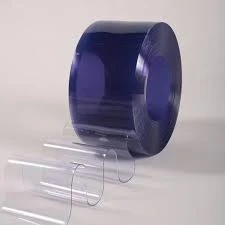
Another advantage emphasized by industry experts is the easy maintenance and cleanliness of plastic curtains. Unlike solid doors, these curtains do not require complex mechanisms or frequent repairs. A simple routine of wiping down the strips with mild detergent can prevent the buildup of grime and bacteria, maintaining hygiene standards essential for compliance with health regulations in cold storage operations.
cold storage plastic curtain
In terms of expertise, the deployment of plastic curtains plays a critical role in managing air infiltration. Professionals assert that strategic installation requires considering factors such as ambient temperature differences, traffic flow frequency, and curtain overlap. A common best practice is to have strip overlap of at least 50%, which ensures comprehensive coverage and efficient temperature partitioning without restricting movement.
Authoritative voices in the industry often advocate for customized solutions tailored to specific operational needs. While standard-sized curtains offer flexibility, bespoke designs cater to unique structural and logistical demands. For instance, bespoke cuts can accommodate irregular door sizes or include features like fire resistance or anti-static properties for specialized environments. Moreover, advanced options with anti-insect formulations or UV filtration capabilities further enhance product offerings to meet diverse industrial requirements.
Trustworthiness is established by manufacturers who adhere to stringent safety standards and possess certifications from recognized bodies. Reputable providers offer product warranties, underscoring their commitment to quality and customer satisfaction. Testimonials and case studies from businesses utilizing plastic curtains affirm the tangible benefits — reductions in energy expenditure, improvements in workflow efficiency, and compliance with environmental standards.
In conclusion, cold storage plastic curtains serve a vital role in maintaining efficient operations within temperature-controlled environments. They are an economical solution that combines energy efficiency, environmental adaptability, and robust design for a variety of applications. By engaging with suppliers recognized for their quality and innovation, cold storage facilities can enjoy enhanced operational efficacy and a higher standard of temperature management, ensuring both product safety and energy savings.