Transparent PVC welding curtains are invaluable tools in industrial environments where safety, efficiency, and visibility must coexist. These curtains not only shield workers from harmful welding arcs but also facilitate a safe and organized workspace that adheres to occupational safety standards. This article delves into the exceptional advantages of transparent PVC welding curtains, highlighting their pivotal role in modern manufacturing settings and presenting a compelling case for their integration in industrial workspaces.
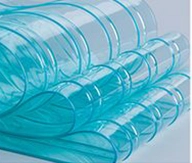
In industries where welding is a core activity, maintaining the safety of workers and ensuring the smooth flow of operations is a top priority. Transparent PVC welding curtains achieve this by creating defined boundaries that protect employees not directly involved in welding tasks. The material, typically treated for flame resistance, acts as a barrier against welding spatter and harmful UV radiation emitted during the process, significantly reducing the risk of burns or eye injuries.
What sets transparent PVC welding curtains apart from other types of barriers is their ability to maintain line-of-sight visibility. In high-paced work environments, it is crucial for supervisors and colleagues to monitor activities without physical intrusion. The transparency of these curtains allows for continuous observation of welding operations, thereby facilitating quick interventions if necessary and ensuring that safety protocols are adhered to.
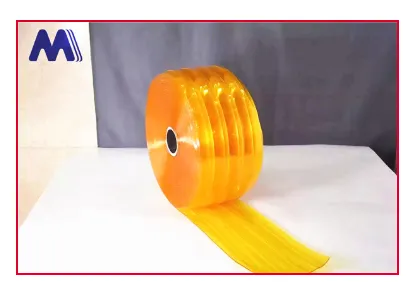
From a technical standpoint, transparent PVC welding curtains are engineered to meet stringent safety standards. They are crafted from high-quality polyvinyl chloride, known for its durability and resistance to temperature extremes. This material is not only effective in providing protection but also ensures longevity, making it a cost-effective solution for businesses aiming at long-term safety strategies.
Moreover, the installation and maintenance of transparent PVC welding curtains are straightforward, adding further value through ease of use. Many of these curtains come equipped with grommets and attachment mechanisms that allow for quick setup in any workspace. Their low maintenance requirements come as a relief to facility managers, as they can be easily cleaned and do not require frequent replacements.
transparent pvc welding curtain
In addition to their practical benefits, transparent PVC welding curtains contribute to the aesthetic organization of a workspace. They help create a professional and orderly environment by minimizing clutter, thus promoting a more efficient workflow. Furthermore, their adaptability in various settings, from small workshops to large manufacturing plants, underscores their versatility as a safety solution.
The expertise behind manufacturing these curtains relates back to comprehensive research and development, focusing on workplace safety innovations. Industry experts continuously work on improving the transparency, strength, and flame-retardant properties of the materials used. As a result, the industry has witnessed the creation of welding curtains that not only meet but exceed existing safety standards, offering peace of mind to employers and employees alike.
Trustworthiness is central to the adoption of transparent PVC welding curtains. Companies prioritizing employee safety often conduct rigorous evaluations of protective equipment before deployment. Independent testing and certifications from relevant safety bodies further bolster trust in these products, assuring companies that they are choosing a reliable protective measure for their workforce.
With the integration of transparent PVC welding curtains, workplaces can effectively enhance safety and efficiency without compromising on visibility and monitoring capabilities. These curtains are not just safety barriers; they are essential components of a comprehensive safety strategy that supports both productivity and well-being in industrial environments. As the nature of manufacturing evolves, these innovations will remain at the forefront, aiding companies in keeping pace with safety requirements and operational demands.